Recognizing the Significance of Welding Examination in Ensuring Structural Honesty and Security Across Different Industries
Welding examination is an indispensable procedure that safeguards structural stability and safety and security throughout varied industries. As we explore the complexities of welding examination, the inquiry arises: what are the most important variables that add to effective assessment procedures?
Duty of Welding Inspection
While the stability of bonded structures is paramount to safety and performance, the duty of welding inspection can not be overstated. Welding examination acts as a critical quality assurance process that makes sure the adherence to established criteria and requirements throughout the welding procedure. By systematically examining welds for flaws, variances, and non-compliance, inspectors play an important function in protecting the stability of frameworks across various industries.
Welding inspections incorporate a series of tasks, from pre-weld analyses to post-weld examinations. These evaluations not just determine prospective problems before they intensify yet additionally improve the general dependability and life-span of bonded components. Welding Inspection Milwaukee. Evaluations assist to verify the ability and expertises of welders, guaranteeing that welding treatments are implemented correctly and materials work
Moreover, a strenuous examination procedure cultivates compliance with regulatory demands and sector requirements, lessening the threat of disastrous failures. By advertising a culture of safety and liability, welding evaluation adds dramatically to both functional and financial efficiencies. Altogether, the duty of welding assessment is essential, as it underpins the top quality, safety, and durability of welded structures important to contemporary framework and industry.
Kinds Of Welding Evaluations
Recognizing the various kinds of welding evaluations is crucial for keeping the quality and security of bonded structures. Welding inspections can be classified into numerous types, each offering a particular purpose in the analysis process.
Aesthetic inspection is one of the most essential kind, involving a mindful examination of the welds with the naked eye or with magnification. This approach aids determine surface area issues such as cracks, incomplete blend, or too much spatter.
Next is non-destructive screening (NDT), which consists of methods such as ultrasonic testing, radiographic screening, and magnetic particle testing. These approaches allow assessors to assess the integrity of welds without jeopardizing the material's structure. Ultrasonic testing makes use of high-frequency sound waves to identify internal defects, while radiographic screening utilizes X-rays or gamma rays to imagine inner weld characteristics. Magnetic particle screening, on the various other hand, is reliable for discovering surface and near-surface stoppages in ferromagnetic products.
Devastating screening, though much less common, includes physically evaluating samples to comprehend the weld's mechanical residential or commercial properties. Each sort of inspection adds to a detailed assessment, guaranteeing that welding meets sector requirements and security requirements.
Industry Requirements and Rules
Establishing industry criteria and guidelines is important for ensuring the safety and security and integrity of bonded frameworks. These requirements function as benchmarks for quality, efficiency, and security, guiding suppliers and inspectors in the execution of welding processes. Different companies, such as the American Welding Society (AWS) and the International Organization for Standardization (ISO), have actually developed detailed criteria that dictate treatments for welding techniques, qualification of welders, and examination techniques.
Conformity with these policies not only boosts the quality of welds yet also reduces i was reading this threats related to structural failings. Particular codes, such as the ASME Central Heating Boiler and Stress Vessel Code, rundown requirements for the building and construction of pressure vessels, ensuring they can hold up against functional tensions. Furthermore, nationwide and regional regulations commonly mandate adherence to these industry standards, strengthening their significance across sectors like building and construction, aerospace, and automotive production.
Routine updates to these standards mirror developments in innovation and welding techniques, making sure that security measures stay pertinent. Thus, a detailed understanding and implementation of these criteria is vital for welding professionals, cultivating a culture of safety and high quality in bonded structures.
Effects of Poor Inspections
Insufficient assessments can lead to extreme repercussions in the welding industry, weakening the really guidelines and criteria made to make certain safety and structural integrity. The repercussions of bad inspections can manifest in different types, from prompt safety and security hazards to long-lasting architectural failings.
Additionally, poor inspections can taint a firm's reputation and lead to legal consequences, including fines and lawsuits. Non-compliance with recognized requirements not just jeopardizes the integrity of tasks however additionally lessens consumer count on in the brand. Additionally, the financial implications can be shocking, encompassing both straight prices associated with fixings and indirect prices such as lost company chances and enhanced insurance premiums. Eventually, the ramifications of poor examinations prolong beyond individual jobs, impacting industry-wide criteria and public assumption, therefore stressing the essential demand for reliable and rigorous welding inspections.
Ideal Practices for Effective Assessments
Efficient welding evaluations are paramount to ensuring the integrity and safety of bonded frameworks. To accomplish optimal outcomes, assessors must abide by a number of ideal practices that improve the assessment process.
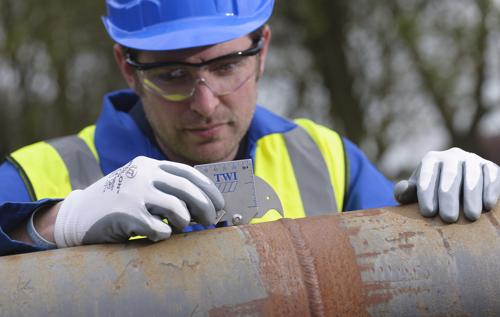
Secondly, inspectors should have the essential qualifications and certifications relevant to the welding procedures and products being taken a look at. Continuous training and professional development are vital to remaining upgraded on industry standards and technical innovations.
Furthermore, using suitable evaluation tools and strategies, such as visual assessments, ultrasonic testing, and radiographic evaluations, is essential for identifying issues that can endanger structural integrity.
Lastly, thorough paperwork of the assessment procedure is necessary. By implementing these ideal methods, organizations can considerably enhance the effectiveness of their welding evaluations and ensure secure, dependable procedures.
Conclusion

In final thought, welding inspection is vital for maintaining architectural stability and safety throughout numerous sectors. Focusing on effective welding inspections is vital to guarantee the safety and security of workers, properties, and overall operational integrity.

As we explore the intricacies of welding assessment, the question develops: what are the most critical aspects that contribute to reliable assessment processes?
Welding evaluation offers as an essential top quality control process that guarantees the adherence to developed standards and specs throughout the welding procedure. In sum, the duty of welding evaluation is indispensable, as it underpins the high quality, safety, and durability of bonded structures necessary to modern facilities and sector.
Various companies, such as the American Welding Culture (AWS) and the International Organization for here are the findings Standardization (ISO), have developed detailed requirements that dictate procedures for welding techniques, certification of welders, and inspection strategies.
Eventually, the ramifications of bad inspections prolong past private tasks, affecting industry-wide requirements and public assumption, therefore highlighting the important requirement for reliable and rigorous welding inspections.